Automated Business Processes Keep Medical Equipment RunningAutomated Business Processes Keep Medical Equipment Running
By combining business-process automation and mobile technology, Spacelabs Medical is improving service and generating more revenue.
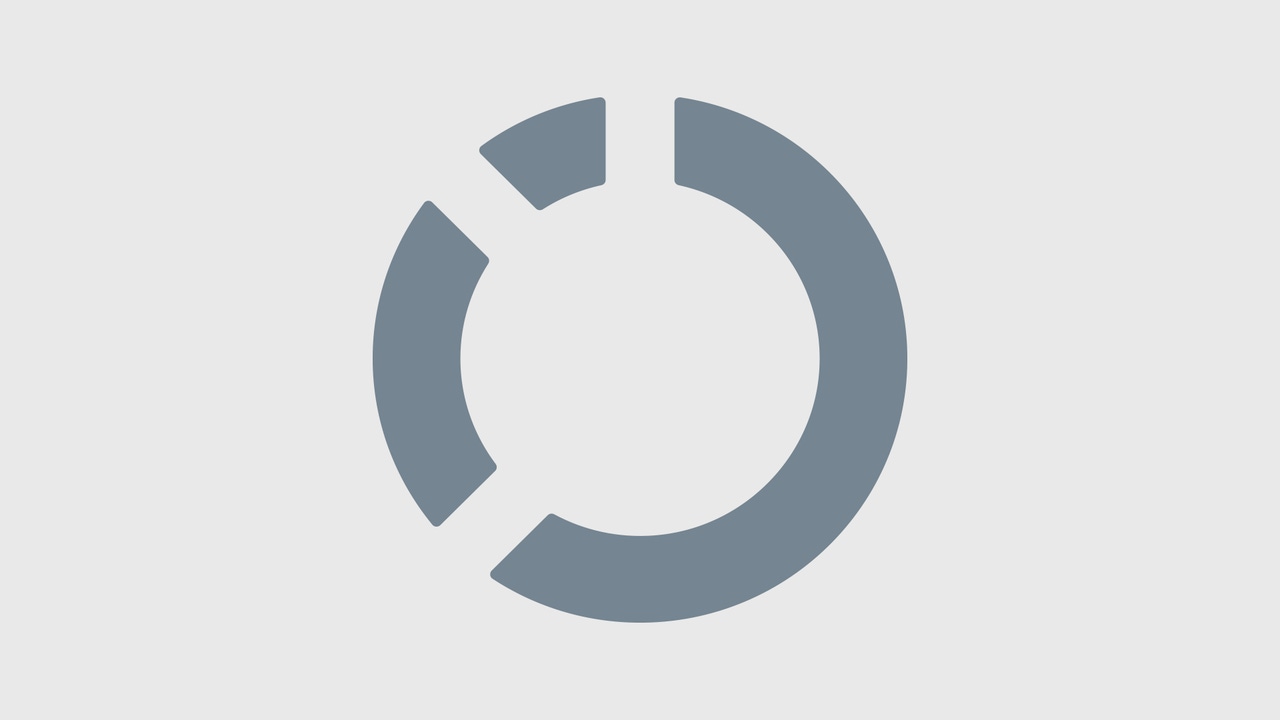
A supplier of intensive-care equipment to hospitals is breathing new life into its field service force with a combination of automated and mobile business processes.
For the last year, Spacelabs Medical (Canada) Inc. has been able to marshal a variety of back-office systems to extend a set of business processes, such as work-order updating and invoicing, to service technicians as they make their rounds. The technicians are constantly on the move and make several calls a day, maintaining 17,000 pieces of medical and patient monitoring equipment across Canada.
Paul Roy, Spacelabs national service manager, says his 10-person field force is racking up 5% more revenue because they not only promptly file completed work orders, allowing same-day invoicing instead of a slow, two-week postal process, but capture extra work done at many sites. It's not uncommon for a customer to turn to a technician and say, "While you're here, why don't you fix this," Roy says. In the past, such work either generated a second set of forms, adding to the service technician's paperwork, or was discreetly swept under the rug as the technician returned to his home office. Now, with a Fujitsu tablet PC able to display a simplified form, he can fill out a work order on the spot and collect a customer signature. Both data and digitized signature are sent back to the central MFGpro business-process application during the technicians' periodic connection to the central office.
Roy says the revenue gain is significant enough to warrant considering deploying the mobile business-process application to Spacelabs' 75 U.S. service technicians. Used principally for scheduling, conveying work orders, and invoicing thus far, the application could serve a variety of additional service needs, Roy says. Right now, it's difficult to supply technicians with much more than the service history of a particular piece of equipment based on a serial number the technician keys in. There's no remote diagnostics possible or recommendation on how to repair, say, an intensive-care patient monitor or other life-saving piece of equipment that may need particular adjustments in its life cycle.
Spacelabs would like to make MFGpro available wherever the technicians go inside the hospital, thus giving them a mobile reference machine that's able to search for solutions to particular problems. "In the future, we're looking to add trouble-shooting documentation. Key-in a description of the problem and get instructions on what to do," says Roy. What would be most useful is if the application became a wireless application, delivering information exactly where it's needed.
But there's little point in making it a wireless application at this point. "In a hospital, you can't use wireless," says Roy, so technicians have to get out of the sensitive areas in which they typically work--intensive care rooms, neonatal-care and cardiac-care wards, and emergency rooms--to synchronize their mobile application with the central server the old-fashioned way, by connecting their tablets to a phone line and dialing an Internet connection.
MFGPro actually runs as a hosted system at Adesso Systems Inc., whose Instant Mobility platform served as the core of the customized MFGPro. Customers may host such an application themselves, if they choose. Either way, the charge is subscription-based, $20 per user per month. Spacelabs created the idea for the application and Adesso built it in about six weeks, says John Landry, chief technology officer at Adesso.
MFGPro connects to a variety of ERP backend systems and databases to enable business processes. The Instant Mobility core platform can deliver information to a variety of mobile devices, including smart phones, handhelds, laptops, or Pocket PCs, as well as tablet PCs. Landry says the Instant Mobility platform can host applications that receive RFID data from the field and mobilize business processes in response to it.
The MFGPro application works as a Web service. It can synchronize data between the field technician either synchronously, with both client and server in direct contact, or asynchronously, such as updating a technician's schedule the next time he's connected, which may be several hours after the update first becomes available.
Roy says MFGPro's scheduling feature allows service technicians to get updated information on work orders more quickly, but wasn't meant to significantly increase the number of visits they could make. They were already executing the sometimes widely dispersed visits as rapidly as possible, he says.
But there has been a gain in the number of completed work orders submitted correctly. A rules engine doesn't allow one to be sent unless all the required information is present. "There's been a big time savings in the processing of paperwork, which gives the staff time to do more reasonable things," including reducing stress, Roy says.
About the Author
You May Also Like