Less With LessLess With Less
Spend management is the latest supply-chain buzz - for good reason. But has the pendulum swung too far?
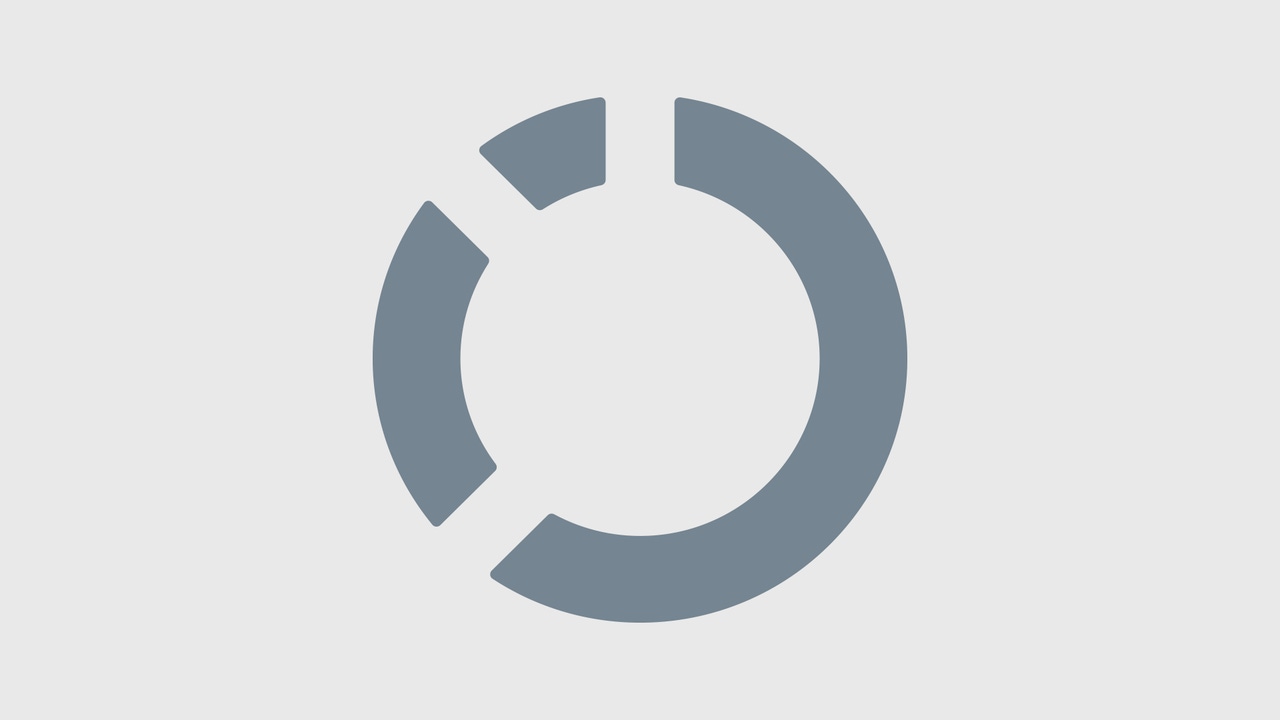
Shortsighted cost cutting may be doing untold damage to the future well-being of your supply chain.
As newspaper headlines attest, the U.S. economy's productivity figures over the past couple of years have been phenomenal. The increase in productivity has come despite reductions in the work force and capital spending and record low levels of inventory. Some of the productivity gains have come at the expense of supply chains supporting the manufacturing and service sectors. The squeeze has been felt across the board — from supply chain technology vendors to manufacturing firms and logistics companies.
In keeping with the times, some supply chain management (SCM) technology vendors have simplified and streamlined their features to showcase "spend management," which seems to be a euphemism for cost cutting and budget control. Although cost cutting across the board was long overdue after the profligate spending of the late 1990s, I fear that the pendulum now has swung too far the other way.
Preparing for Marathons
I've written numerous columns reiterating the point that enterprisewide supply chain technology initiatives should be like marathons: Companies need to prepare for the long haul. Companies seeking to gain strategic advantage from supply chain technology initiatives need to spend time on re-engineering business processes — reducing the delivery and manufacture cycle times while increasing customer choice and convenience — to span not only internal departments but supply-chain partners. Supply-chain technology initiatives rarely succeed unless these business processes have been re-engineered first.
Over the past few years, however, these fundamental drivers of supply chain initiatives have given way to cutting costs — at all costs! Companies have positioned themselves for running sprints and have shed too much human and technical capital needed to prosper once the growth cycle marathon starts.
The cost-cutting measures of the past few years, while positively impacting the bottom lines of corporations, may have damaged the supply chain collaborative mindset beyond repair in certain industries. As the economy rebounds, the focus of SCM technologies will shift from "spend management" to reducing manufacturing cycle times and increasing customer choice and convenience. Corporations that have cut too deep and alienated their supply chains will find themselves unable to gain any significant benefit from SCM technology initiatives.
Squeezing The Supply Chain
Over the past few years, supply-chain partners of the giant corporations and original equipment manufacturers (OEMs) in the manufacturing, retail, and service sectors have been squeezed on prices like never before. Supply-chain partners had to meet unilateral cost reduction targets for goods and services mandated by the dominant OEM. SCM technology initiatives that would have improved visibility and reduced waste, cycle time, and costs across the supply chain were the first victims of the cost-cutting spree. Tangible benefits from these types of SCM technology initiatives take time to measure and validate. The urgency of cost cutting and the need for quick results killed most long-term initiatives.
Those companies that continued with their SCM initiatives found that the supply-chain partners who had to implement a portion of the SCM technology initiative frequently negotiated putting a stop to their portion in exchange for meeting OEM-mandated cost-reduction targets. Unfortunately, this had the inadvertent effect of rolling out an SCM initiative with major technology gaps across the supply chain. Obviously, increased visibility and improved supply-chain response-time goals are impossible to achieve with the missing supplier components. A vicious cycle results, as the OEM further mandates new supplier cost cuts as a way to meet the promised return on investment (ROI) from past SCM investments. Those supply-chain companies that aren't dominant or lack OEM power have been forced to cut to the bone or have gone out of business.
There's a silver lining to this black cost-cutting cloud: A few "enlightened" companies are cutting costs while maintaining a collaborative spirit across their supply chains. It is these companies, in my opinion, that will be primed to take advantage of the rebounding economy.
Bucking The Trend
Faced with the economic downturn, lagging sales, and excess inventory, some corporations invited their supply-chain partners to collaborate on generating ideas on how to survive the tough times. Surprisingly, these corporations found that suppliers were able to identify process improvements that reduced costs across the supply chain. In some instances, process improvements supported by technology were able to immediately generate tangible benefits.
Still, when these measures weren't enough, cost-cutting targets for suppliers were arrived at jointly through negotiation, as opposed to OEM or dominant partner mandates. The "enlightened" corporations made the effort to ensure that all supply-chain partners felt the "pain" of cost cutting equitably. Whether the cost-cutting measures were equitable is debatable, but the more important result from this exercise was that the supply-chain partners didn't lose the collaborative spirit with the dominant partner. This factor will be critical for successful SCM implementations as the economy rebounds. Corporations and their supporting supply chains that cut costs too deeply may have lost precious subject matter experts and knowledge necessary to implement SCM initiatives that seek to achieve goals beyond "spend management."
Losing Knowledge
To successfully implement and realize tangible benefits from SCM technology initiatives, a corporation needs employees who have detailed knowledge on how raw materials are sourced, manufactured, and distributed, and how the end customer is serviced (industrial, retail, or consumer). These employees in turn need to be complemented with supervisors and managers who understand how the specific supply-chain processes interact between departments within the firm and across the supply chain.
My personal experience in the automotive sector has been that this knowledge takes years to develop. Given the huge amount of raw materials and service inputs that go into making a car, understanding the supply-chain processes that produce a car is a complex, multiyear endeavor. Similar parallels exist in the service and retail sector supply chains.
The recent cost-cutting measures unfortunately have decimated the middle management and supervisory ranks across many corporations. Although layoffs may have been necessary for short-term survival, these corporations have lost valuable supply chain knowledge that they need in order to prosper during the economic recovery. It seems logical that corporations that kept the collaborative spirit alive during the economic downturn would be positioned to get a head start on their competition during the growth phase.
Outsourcing various functions within a corporation may have further eroded institutional knowledge required for SCM reengineering. Admittedly, purely technical functions that have no business process content can and should be outsourced. Technical personnel supporting legacy SCM systems aren't valuable for their technical skills, but for their intimate SCM business process knowledge. And it's cause for alarm when functions with a high degree of business process knowledge are outsourced.
Getting a single corporation's employees to collaborate for an SCM reengineering effort is challenging. (See Resources.) Imagine how difficult it will be to get them to cooperate with outsourced partner participation — if they will at all.
A Head Start
Doing "more with less" and "faster, better, and cheaper" seem to be the mandates of the past few years. But contrary to the prevailing trend of indiscriminate cost cutting, these goals are realizable only if a company first spends resources to re-engineer the supply chain and money to implement technologies in pursuit of those re-engineering goals. The experience of the past few years, however, has been that companies want the benefits without investments and a commitment to a collaborative supply chain.
I invite you to let me know what you think about the assertions in this column. Is my experience isolated to the automotive sector, or is this a general trend across other industries as well? The gains made in the last decade in creating collaborative supply chains in different industries seem to have come unglued during the recent economic downturn.
The prevailing wisdom for SCM technology initiatives seems to be to spend during growth and cut during economic downturns. A contrarian approach — keeping a collaborative mindset toward cost cutting during the downturn — offers a significant competitive advantage.
RAM REDDYTactica Consulting Group
About the Author
You May Also Like