Chemicals: A Tech Formula For Cost ControlChemicals: A Tech Formula For Cost Control
IT helps chemical makers rein in costs to stay competitive in commodity market
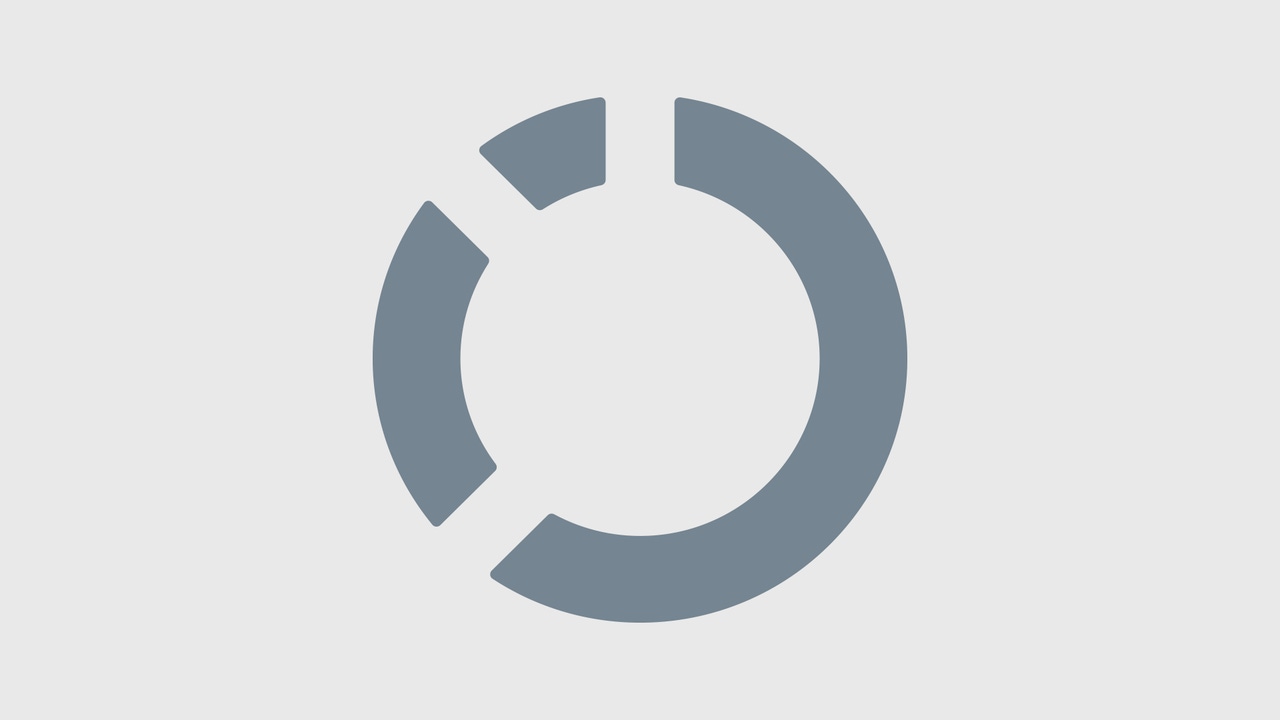
As oil prices skyrocket, chemical manufacturers, for whom petroleum is a critical raw material, find themselves yet again looking for more efficient ways to run their companies. The threat from higher oil prices comes just as chemical makers and their IT departments thought they were seeing light at the end of the economic tunnel after the recession and the rapid commoditization of many chemical products in recent years.
Air Products and Chemicals Inc., a maker of specialty gases and other chemicals, is only now coming to grips with the commoditization of many of its products by becoming more price-driven. "It's been a difficult transition for us," says Alan Jeffery, the company's continuous improvement manager for global IT. "We have a significant focus on process and on cost containment."
Air Products used to be run as a loose collection of business units, many with their own applications and IT infrastructures. The emphasis now is on consolidating those disparate units into a series of standard global business processes such as supply-chain management, finance, and manufacturing, using SAP applications the company began implementing in 2002 as a framework, Jeffery says. IT is transforming itself into a central service provider for those processes.
PolyOne Corp., which makes polymers, colorants, and other chemicals for making plastics, is likewise simplifying its business processes and the IT that supports them to cut costs. Standard processes for closing the company's books each month have replaced the disparate processes once used by regional financial controllers. A new central process for ordering raw materials has cut operating costs and boosted volume-purchase discounts. Like Air Products, PolyOne is leveraging SAP applications as the backbone of its revamped operations, says John Connors, global business-systems director at PolyOne.
None of this gives IT a blank check. PolyOne has cut IT spending by retiring noncritical systems, trimming third-party maintenance and telecommunications contracts, and reducing personnel. "But we're as productive as we were before because we've reduced the complexity of our IT landscape," Connors says. "It's forced us to focus on the things that are truly important to the enterprise."
Air Products' IT budget has risen in recent years because of the SAP project. This year's was approved with a 7% increase, but so far spending has been flat, says Jeffery, who expects the budget to decrease in coming years. The recent elimination of some 600 of 2,000 applications made possible by the SAP system will make that easier.
INDUSTRY LEADERS Company Revenue in millions Income (loss)
in millions Bayer Corp. $10,999 -- PPG Industries Inc. $8,756 $494 Ashland Inc. $7,518 $94 Air Products and Chemicals Inc. $6,297 $397 Eastman Chemical Co. $5,800 $267 Engelhard Corp. $3,714 $324 Lubrizol Corp. $2,052 $91 PolyOne Corp. $1,965 ($4) Cabot Corp. $1,795 $77 Millennium Chemicals Inc. $1,697 ($184) Noveon Inc. $1,135 $13 Arch Chemicals Inc. $1,009 $27 Grain Processing Corp. -- -- Royster-Clark Inc. -- -- Financial data is from public sources and company supplied.
Revenue is for latest fiscal year.
Dashes indicate companies requesting financial information not be disclosed.
SNAPSHOT INSIDE COMPANIES Average portion of revenue spent on IT 2% Companies using radio-frequency identification 7% Companies globally sourcing products and supplies 86% HOW COMPANIES DIVIDE THEIR I.T. BUDGETS Hardware purchases 20% IT Services or outsourcing 18% Research and development 3% Salaries and benefits 28% Applications 17% Everything else 14% INDUSTRY FINANCIALS Average year-over-year revenue change 11% Average year-over-year net income change 183% DATA: information RESEARCH
See year-over-year shifts in business-technology practices for this industry.
Compare and contrast this year's data with last year's.
About the Author
You May Also Like