RFID Tagging Is More Than Slap-And-ShipRFID Tagging Is More Than Slap-And-Ship
A study by ARC Advisory Group finds that companies have to do more than put RFID tags on goods just before they get shipped out.
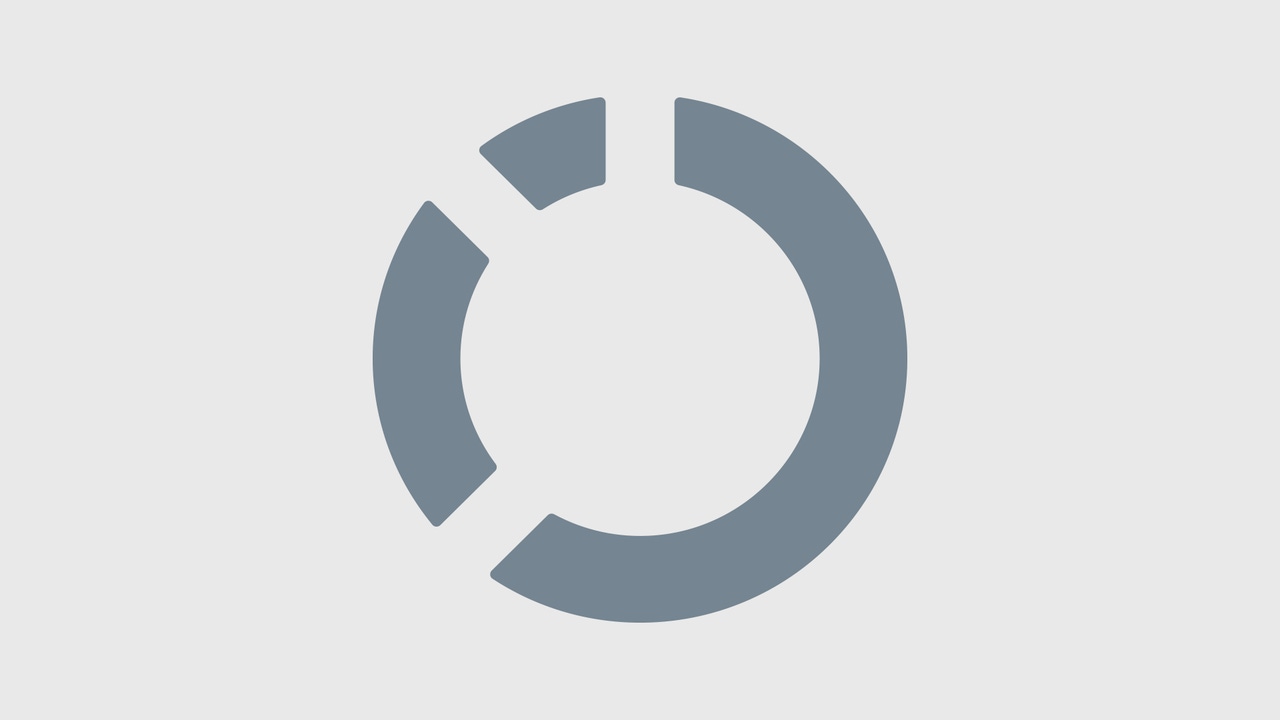
The simple "slap-and-ship" method of radio-frequency identification tagging--which involves putting the RFID labels on goods just before they get shipped off to customers--isn't as common or as easy as you may think, according to a study issued this week by supply-chain research firm ARC Advisory Group.
In fact, the study found that 85% of RFID tags are being applied at distribution centers using processes that require more automation and more process variation than required in the slap-and-ship method. ARC talked to 24 companies primarily from the food and beverage and the consumer-products industries, as well as a third-party logistics company and a packaging company, that are actively investing in electronic product code RFID.
The companies are applying tags in several different ways. Some are manually affixing tags, which is typically done at a value-added service station in a distribution center, says Steve Banker, service director for supply- chain management at ARC. Others are manually tagging at ad hoc stations set up on the receiving dock. In other instances, companies are affixing tags on pallets and cases as they move along conveyor-belt systems. Some have set up gates that redirect goods to a side station if tags can't be read. Finally, some companies have opted to pre-print RFID tags and apply them to cases when goods are picked. This "pick-to-cart" process is typically used for mixed pallet orders. Generally, the three methodologies are not exclusive and companies can choose to use them interchangeably in the same distribution center, Banker says.
Campbell Soup Co. is one company affected by this month's Wal-Mart deadline that, for now, is using the slap-and-ship method, which has delivered a 96% success rate for case reads at the company, said Mark Engle, senior director of IT, at the EPC Global U.S. Conference in September. But tagging at Campbell's 212,000-square-foot facility in Texas illustrates that the slap-and-ship process isn't as simple as it sounds. For example, Campbell has been building optimized case loads and working with air gaps in cases of liquids and metals to improve tag readability. The company also set up a conveyor line and a manual line in the repacking area for tagging.
Says Banker: "The [slap-and-ship] process is more complex and there is more diversity in the way companies are doing this than generally realized."
About the Author
You May Also Like